Over the past two decades, as software and data analytics technologies have rapidly advanced year over year, users of Transportation Management Systems (TMS) have made significant strides in managing day-to-day logistics operations.
But have these advances truly led to greater efficiency, throughput, and improved service levels? To what degree is business today ahead of where it once was, and is productivity really being improved?
The answer may be “yes” compared to the 2010s. Companies with sophisticated TMS systems installed have without question gained the ability to manage larger volumes, improve end-to-end visibility, and achieve a higher macro-level view of service performance.
However, more sophistication yields a better ability to monitor and measure performance. And with recent advancements, even more critical questions remain:
- 1.Were deliveries consistently on time? How did we measure this?
- 2. Were the right trucks used as prescribed? Are we optimizing our fleets?
- 3. Did warehouse or plant operations become more efficient? Where are the gaps?
- 4. Were deliveries made to the correct location with accurate Proof of Delivery (POD)?
- 5. Were shipments delivered on time and in full?
- 6. Was freight cost effectively reduced?
The answers to these and many more other potential questions aren’t always a clear “yes.” While there has been progress from 2010 to 2024, and despite the immense improvements in technology and measurement, success rates are still only around 80% on-time delivery. And for the more complex scenarios captured in the questions posed above, they hover near 60%.
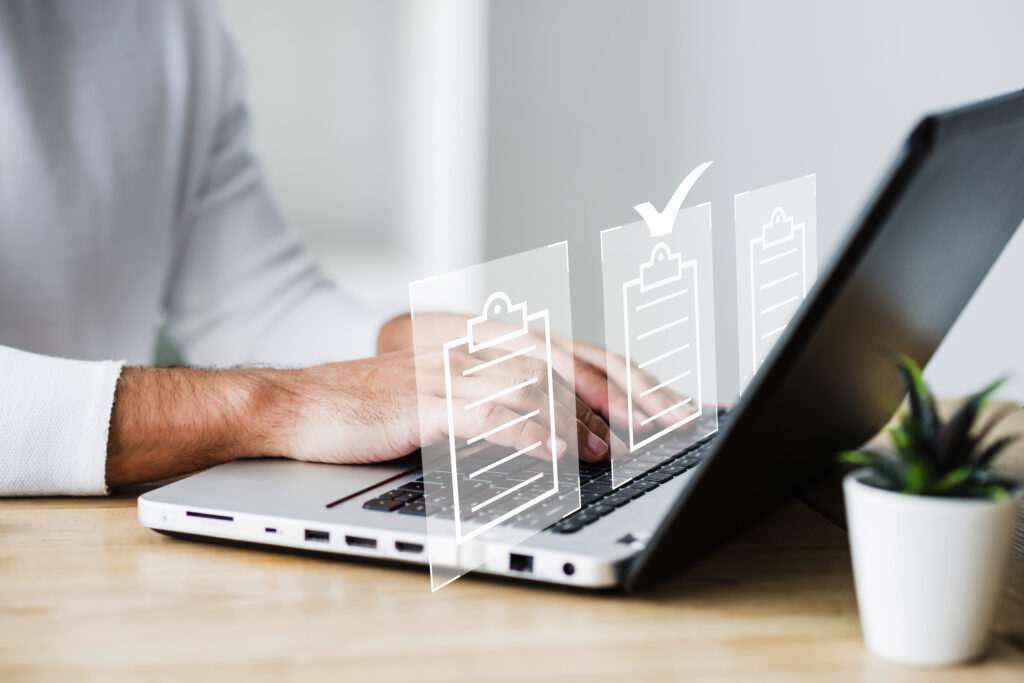
ERP systems can report on what happened after the fact, but often failing to provide the data needed in real time. The same is generally true with TMS systems, as well as others so-called “backend systems of record.”
So why do TMS solutions still struggle to achieve near-perfect accuracy, even with sophisticated algorithms and tools? The answer lies in latency, or the time it takes data to transfer across a network or supply chain ecosystem.
Real-time event capture is key to improving service levels.
TMS solutions rely on assumptions; the assume that the right truck will arrive at the right time … that the dock will be available as planned … and that deliveries will occur according to schedule. But what happens when these assumptions aren’t met? The TMS repeatedly runs its algorithms, assuming the original conditions, leading to rescheduling and a cycle of inefficiencies. This process impacts the most optimized plans at a macro level. And soon, the business is paying the price, because as well as know, in business time … is money.
The root cause of the problem of latency, or unhelpul delay, lies in how the events are fed into TMS solutions. These delays—whether minutes, hours, or days—can cause many unwelcome business problems. From fundamental disruption of how a plan is executed, to valuable assets being left unused, or unproductive time among people, poor execution can lead to waiting trucks, and delayed deliveries. And all this can have a negative impact on valuable relationships.
What’s needed is a shift. While TMS systems should plan for trucks, production inventories, and capacities, execution should be left to real-time, event-driven systems. These systems must provide playbooks at every stage of execution, making immediate decisions based on real-time events, powered by AI.
AI-powered engines can react to disruptions instantly. Whether a truck fails to arrive on time, or a loading bay breaks down, these systems make decisions without waiting for human intervention. They also address issues like overload/underload tolerance, route deviations, and unauthorized stops in real time without rerunning TMS algorithms.
Intelligent process playbooks, such as those developed by Autoplant, define for each potential deviations at every stage, and most importantly executed in real time, are key to achieving leaner, more efficient, and on-time deliveries.
Autoplant’s real-time execution platforms can ensure accurate deliveries without compromising the macro plans optimized by TMS. Autoplant uses IoT sensors to monitor operationsat every stage—from the yard to the warehouse, to the road—detecting deviations and utilizing intelligent playbooks to guide the next steps.
With AutoPlant, the promise of a zero-latency truck-delivery platform is being realized, improving all key performance indicators that TMS systems strive to enhance
Author – (Suresh Sachdev, CEO, AUTOPLANT)